Electroless nickel
Top provider of high-end electroless nickel plating.
ElectroLess Nickel Plating Overview
Electroless nickel plating is a form of alloy treatment process that deposits a nickel-phosphorous without need for an externally applied electrical current. The electroless nickel plating process occurs from a chemical reduction of the nickel ions within the electroless nickel solution onto a metallic substrate rather than deposition of the ions from an applied current. As a result, the electroless nickel deposit is free of many of the problems associated with traditional electrolytic nickel including edge buildup and non-uniform coating. Electroless nickel deposits are extremely uniform, corrosion and erosion resistant and provide excellent lubricity.
Electroless Nickel Plating Details
Electroless Nickel plating is a process of chemical reactions (no electrical current) used to create an even/uniform layer of amorphous alloy of nickel and phosphorus that mirrors the surface finish of the part that can be plated on non-conductive substrates.
Metal Chem Inc. has developed a process to meet the requirements of MIL-C-26074, ASTM B733 & AMS 2404.
MIL-DTL-26074 This specification covers the requirements for medium and high phosphorous electroless (autocatalytic chemical reduction) deposition of nickel-phosphorous alloy coatings on metal and composite surfaces.
ASTM B733 This specification establishes the requirements for autocatalytic (electroless) nickel-phosphorus coatings applied from acidic aqueous solutions to metallic products for use in engineering functions operating at elevated temperatures. The coatings covered here are alloys of nickel and phosphorus produced by self-sustaining autocatalytic chemical reduction with hypophosphite.
AMS 2404 This specification covers the requirements for electroless nickel deposited on various materials. This deposit has been used typically to provide a uniform build-up on intricate shapes, to improve wear and/or corrosion resistance, or to improve solderability on or for selected materials, but usage is not limited to such applications. The deposit has been used in service up to 1000 Degrees F (540 Degrees C) although wear and/or corrosion resistance may degrade as service temperature increases.
Mid Phosphorus coatings plated in a bath that contains between 6% to 9% phosphorus content. Excellent corrosion resistance, excellent for heavy build up. Parts using this coating exhibit increased hardness which can be increased through heat treatment and moderate wear resistance. Corrosion resistance is good when used in both high pH and acidic environments due to a lower porosity from the higher percentage of phosphorus. For applications that use mid phosphorus electroless nickel plating, the following guideline can be used: 6% to 9% for industrial applications, 5% to 9% for electronics, and 5% to 7% for decorative applications.
High Phosphorus coatings are plated in a bath that contains between 10% to 14% phosphorus content. Parts using this coating exhibit very high corrosion resistance, increased hardness, ductility, and stain resistance. High phosphorus electroless nickel plating is preferred for oil drilling and coal mining parts that will be exposed to highly corrosive acidic environments. Good corrosion resistant, not recommended for heavy build.
Electroless Nickel plating is ideal for industries that need heavy-build applications. Metal Chem Inc. has received dozens of approvals for projects within the following industries:
- Aerospace
- Firearms
- Military & Defense
- Oil & Gas
- Medical Devices
- Marine
Nickel plating can add durability, hardness, conductivity, and heat-resistance to your product, in addition to protecting against corrosion and enhancing its aesthetic appeal. Electroless nickel plating offers numerous advantages over traditional electrolytic nickel plating, including:
- Corrosion Resistance
- Improved EMI Shielding
- Hardness & Durability
- Enhanced Lubricity
- Increased Ductility
- Greater Coating Versatility
- Salvageability
When choosing a new manufacturing partner, vet them carefully to ensure you receive the service and quality you expect. We recommend asking a prospective metal finisher the following questions:
- What substrates are you capable of processing or plating?
- What tooling strategy do you target?
- What best practices does your organization put in place to promote adhesion?
- Do you have demonstrable use of best practices for chemistry and bath control?
- Are you capable of meeting hydrogen embrittlement bake requirements?
- Are the chemicals supplied by a certified chemistry product supplier?
- What post-process inspection measures are in place to ensure thickness, adhesion, and adherence to specifications?
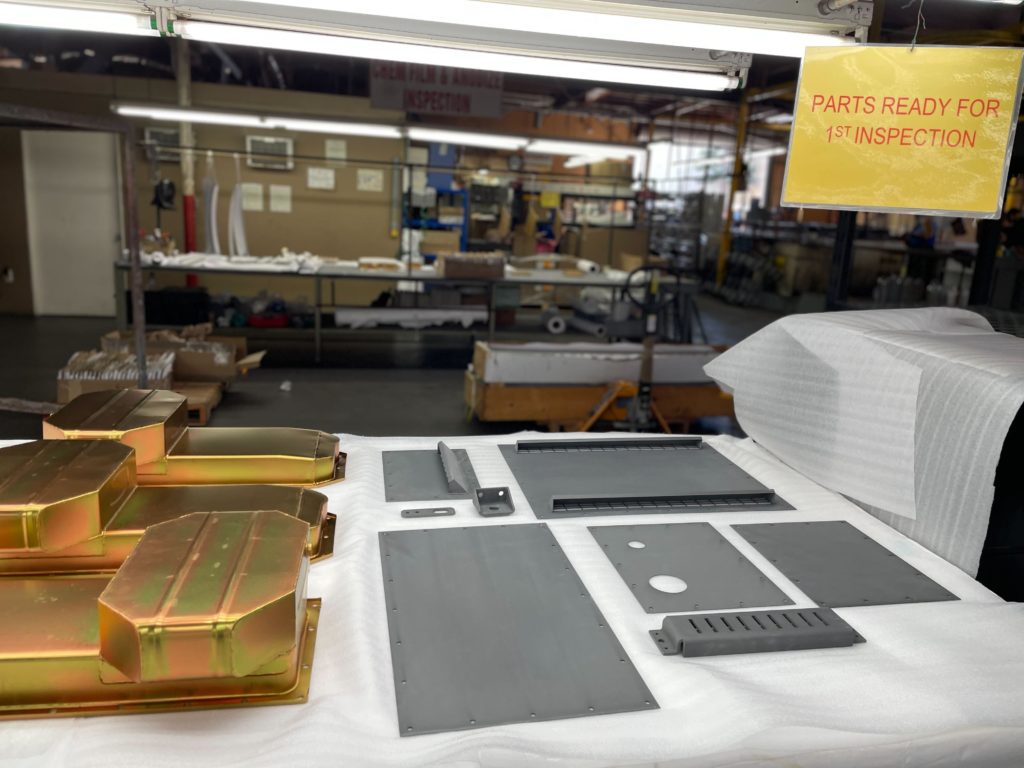
ELectroless Nickel Plating
Quality System
With a facility that boasts over 15,000 square feet, our headquarters includes an in-house laboratory and state-of-the-art technology that’s unparalleled in the metal application industry. You can feel confident that your project is in the hands of experts – our control managers have decades of experience in the science of metal finishing, metal plating, and chemistry.
Quality Criteria for Solution Analysis and Testing
- B10 – Adhesion Testing
- B14 – Conductivity Testing
- B16 – Coating Thickness Measurement.
- B21 – Paint Color and Gloss Testing
- B22 – Solvent Resistance Testing
- B23 – Other Testing In Support of AC7108
Electroless Nickel Quality Control
From Start To Finish
1
Metal Prep + Masking
At Metal Chem, we take the necessary steps to prep your metal prior to the electroless nickel application. If masking is required, our team includes dedicated experts that handle the masking in-house.
2
Metal Application
Metal Chem Inc. maintains the appropriate process controls for our chemical conversion and electroplating processes which require titration, coating weights, pH, and TDS verification.
3
QA Inspection
Most of our quality assurance (QA) testing is done in-house in our qualified laboratory, conforming to ASTM and MIL-SPEC standards. This internal QA assures that you receive quality, consistent results every time.
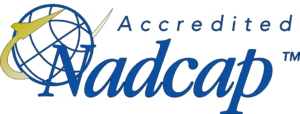
Who We Help
Aerospace & Military Metal Applications Approvals
Since 1991, Metal Chem Inc. has become one of the premiere metal plating and finishing companies in the country. Our NADCAP accreditation has allowed us to proudly fulfill the metal application needs of top technology pioneers in the aerospace, military and naval industries. As an industry leader in spec plating and metal finishing, our team has decades of experience handling complex projects that require a sophisticated level of detail.
Industries We Serve
You ask, we answer
Find answers to the most frequently asked questions about the electroless nickel process.
Electroless nickel plating is an process that codeposits a nickel-phosphorous alloy without need for an externally applied electrical current. The electroless nickel plating process occurs from a chemical reduction of the nickel ions within the electroless nickel solution onto a metallic substrate rather than deposition of the ions from an applied current.
MIL-C-26074 is an electroless nickel plating specification for applying precision coatings to a variety of shapes and sizes. These specifications are typically used within the aerospace, automotive, home electronics, oil & gas, as well as the pharmaceutical industries. Common applications for the MIL-C-26074 (AMS 26074) specification are barrel plating, rack plating, and vibratory plating.
Electroless Nickel plating is ideal for industries that need heavy-build applications. Metal Chem Inc. has received dozens of approvals for projects within the following industries:
- Aerospace
- Firearms
- Military & Defense
- Oil & Gas
- Medical Devices
- Marine
With decades of experience, Metal Chem has the knowledge, experience, and equipment to safely get the job done right. Electroless nickel plating can involve the handling of toxic chemicals and must only be undertaken by metal finishing companies with the ability to handle the chemicals correctly and the ability to work with various regulatory agencies to ensure compliance with environmental and workplace safety laws.
Get in Touch
Phone
(818) 727-9951
info@metalcheminc.com
Address
21514 Nordhoff Street
Chatsworth, CA 91311