Phosphate
Conversion
per ASTM specifications.
Type M
Manganese Phosphate Base
PER MIL-DTL-16232
Type Z
Zinc phosphate base
PER MIL-DTL-16232 / TT-C-490
Zinc Type I
coating weights ranging
from 150 - 500 mg/ft²
Zinc Type V
Coating Weights Ranging
From 500 - 1100 mg/ft²
Phosphate Conversion Overview
Phosphate conversion coating provides a uniform base to apply organic coatings and is used as a protective base for iron and steel subtrates.
Metal Chem Inc. provides zinc phosphate conversion coating to steel and iron surfaces in several applications. Our coating is corrosion-resistant, and prevents galling, scuffing, and seizing of moving parts. It can serve as a uniform, non-reflective finish, or be used as primer for highly decorative painted finishes.
Types of phosphate conversion we offer
In most operations where the corrosion resistance of finished workpieces must be especially high, conversion coatings are applied using zinc phosphate. This approach is widely used in the automotive industry and in certain sectors of the appliance and electronics industries. Similarly, zinc phosphating is often specified by the armed services, especially for equipment that may be exposed to severe environments.
The team at Metal Chem specializes in two types of heavy phosphate coatings for ferrous metals, applied by immersion. These coatings either consist of a Manganese Phosphate or Zinc Phosphate base. Keep reading to learn more about the types of phosphate conversion coatings we offer and applicable ASTM specifications below:
Manganese phosphate coatings – also known as Type M – provide great coating hardness and outstanding corrosion and wear resistance.
Metal Chem provides phosphate conversion coatings according to the MIL-DTL-16232 Phosphate Specifications for the following Type M classes:
- Class 1 – Supplementary preservative treatment or coating.
- Class 2 – Supplementary treatment with lubricating oil conforming to MIL-PRF-16173, Grade 3 or MIL-PRF-3150.
- Class 3 – No supplementary treatment.
- Class 4 – Chemically converted (may be dyed to color as specified) with no supplementary coating or coating as specified.
Zinc phosphate coatings – also known as Type Z – provide excellent bonding capabilities for organic coatings like paints, lacquers, or a CARC military topcoat. When applied to steel or iron, it provides a non-reflective finish which can be dyed to your specification. It also provides corrosion protection to the metal. This coating also provides great corrosion protection to the metal.
Metal Chem provides zinc phosphate conversion coatings according to the TT-C-490 and MIL-DTL-16232 Phosphate Specification for the following Type Z classes:
- Class 1 – Supplementary preservative treatment or coating.
- Class 2 – Supplementary treatment with preservative conforming to MIL-PRF-16173, Grade 3 or MIL-PRF-3150.
- Class 3 – No supplementary treatment.
- Class 4 – Chemically converted (may be dyed to color as specified) with no supplementary coating or coating as specified.
Type I – Zinc Phosphate: Type I coatings are applied by immersion and have coating weights in the range of 150 – 500 mg/ft² (1.6 – 5.4 g/m²)
Type V – Medium weight Zinc Phosphate: Type V coatings are the same as Type I coatings except that the coating weight is in the range of 500 – 1100 mg/ft² (5.4 – 11.8 g/m²).
- Defense: CARC primer, applications that desire non-reflective finish
- Aerospace: moving parts & threads, primer for special coatings
- Automotive: base for coatings, engine, transmission
- Heavy equipment: gears and bearings
- Oil and Gas: primer for components
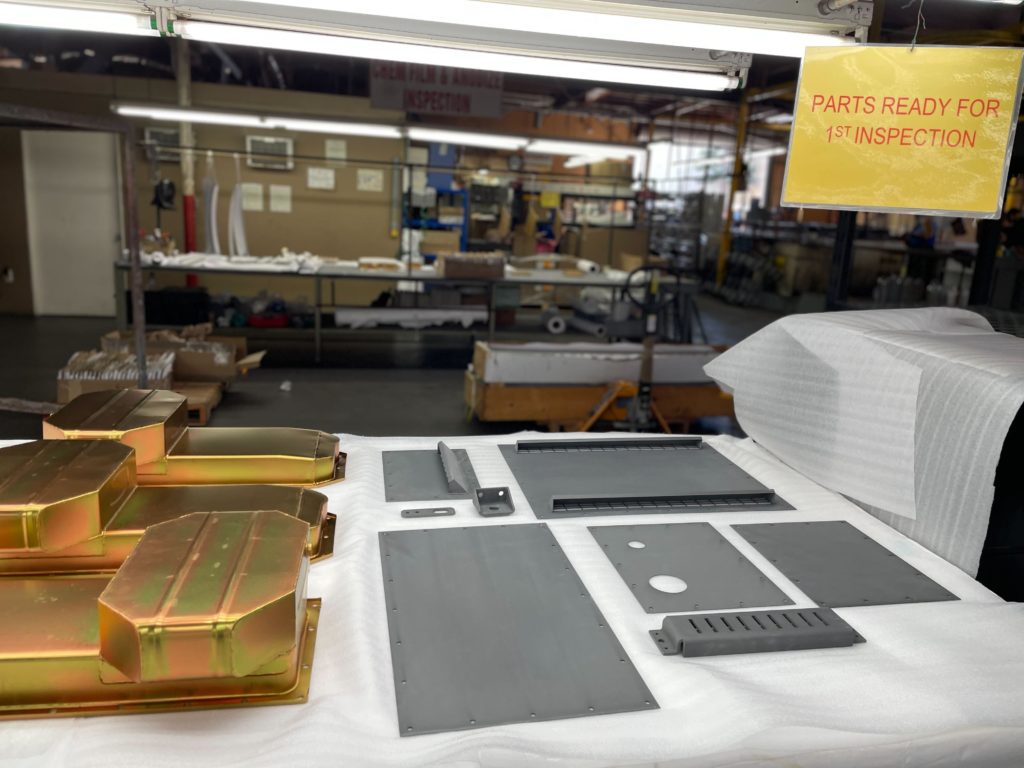
Phosphate Conversion Coating
Quality System
With a facility that boasts more than 15,000 square feet, our headquarters includes an in-house laboratory and state-of-the-art technology that’s unparalleled in the metal application industry. You can feel confident that your project is in the hands of experts – our team of control managers has decades of experience in the science of metal finishing, metal plating, and chemistry.
Quality Criteria for Solution Analysis and Testing
- B10 – Adhesion Testing
- B14 – Conductivity Testing
- B16 – Coating Thickness Measurement.
- B21 – Paint Color and Gloss Testing
- B22 – Solvent Resistance Testing
- B23 – Other Testing In Support of AC7108
phosphate conversion Quality Control
From Start To Finish
1
Metal Prep + Masking
At Metal Chem, we take the necessary steps to prep your metal prior to the phosphate conversion application. If masking is required, our team includes dedicated experts that handle the masking in-house.
2
Metal Application
Metal Chem Inc. maintains the appropriate process controls for our chemical conversion and electroplating processes which require surface cleaning, titration, coating weights, pH, and TDS verification.
3
QA Inspection
Most of our quality assurance (QA) testing is done in-house in our qualified laboratory, conforming to ASTM and MIL-SPEC standards. This internal QA assures that you receive quality, consistent results every time.
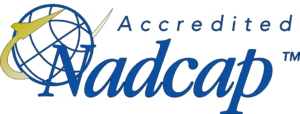
Who We Help
Aerospace & Military Metal Applications Approvals
Since 1991, Metal Chem Inc. has become one of the premiere metal plating and finishing companies in the country. Our NADCAP accreditation has allowed us to proudly fulfill the metal application needs of top technology pioneers in the aerospace, military and naval industries. As an industry leader in spec plating and metal finishing, our team has decades of experience handling complex projects that require a sophisticated level of detail.
Industries We Serve
You ask, we answer
Find answers to the most frequently asked questions about the phosphate conversion process.
Phosphate conversion coating provides a uniform base to apply organic coatings and is used as a protective base for iron and steel subtrates.
MIL-DTL-16232 Phosphate Specifications This specification covers two types of heavy phosphate coating for ferrous metals, applied by immersion. The coatings consist of a manganese phosphate or zinc phosphate base and, when specified, a supplementary treatment.
TT-C-490 Specification This specification covers the cleaning methods and pretreatment of ferrous metals for the application organic coatings (paint, varnish, lacquer, enamel, etc.) and in addition ferrous metals or items having zinc or aluminum surfaces or accessory fabricated parts of zinc or aluminum requiring treatment.
In most operations where the corrosion resistance of finished workpieces must be especially high, conversion coatings are applied using zinc phosphate. This approach is widely used in the automotive industry and in certain sectors of the appliance and electronics industries. Similarly, zinc phosphating is often specified by the armed services, especially for equipment that may be exposed to severe environments.
The list below provides industry application examples for the phosphate conversion process:
- Defense: CARC primer, applications that desire non-reflective finish
- Aerospace: moving parts & threads, primer for special coatings
- Automotive: base for coatings, engine, transmission
- Heavy equipment: gears and bearings
- Oil and Gas: primer for components
The team at Metal Chem specializes in two types of heavy phosphate coatings for ferrous metals, applied by immersion. These coatings either consist of a Manganese Phosphate or Zinc Phosphate base.
Get in Touch
Phone
(818) 727-9951
info@metalcheminc.com
Address
21514 Nordhoff Street
Chatsworth, CA 91311