Powder
Coatings
Top provider of Mil-Specs, Urethanes,
and Epoxy & Polyester Hybrid powder coatings.
Powder Coatings Overview
Powder coating is electrostatically applied as a free-flowing dry powder. Unlike liquid paint, the need for evaporating solvents for paint application is not existent, The applied powder may be thermoset or thermoplastic polymer which is cured at a high temperature with a short dwell time, creating a hard and thicker finish that is more resistant than conventional liquid paint.
Types Of Powder Coatings We Provide
Metal Chem Inc. has an extensive selection of more than 250 stock powder coatings, ready for immediate use. Our complete product line consists of polyesters, epoxies, and hybrids which are formulated and manufactured to meet the highest standard of quality essential to the metal finishing industry.
Key advantages of powder coatings over liquid coatings include providing one of the most durable and economic finishes attainable today. The use of powder coatings offers a solvent-free finishing technique that can help reduce overall line costs and ease cleanup. Powder coatings also help finishers achieve their sustainability efforts, as they have very low to virtually zero VOCs and contain no heavy metals.
Metal Chem Inc. adheres to strict industry standards for MIL-SPEC powder coatings according to the following specification:
MIL-PRF-32348 This specification covers powder coatings for interior steel, aluminum, copper-nickel and bronze equipment, furniture, and electrical box surfaces and on exterior steel, aluminum, copper-nickel, and bronze surfaces exposed to marine atmosphere, high humidity, seawater and weathering.
Polyester Urethane powders are thin film exterior durable coatings that offer good mechanical and chemical resistance properties in the range of 1 to 2.5 mils. These powders can be used both on interior and exterior applications. They are not recommended for films greater than 4 to 5 mils.
Hybrids offer most of the advantages of the epoxies in mechanical and chemical resistance properties and offer improved properties such as greater resistance to yellowing during cure, better transfer efficiency, and cleaner, brighter colors than many epoxy formulations. They are sometimes more economical than epoxies but do have less solvent resistance. Though they are better than epoxies, hybrids are not recommended for exterior exposure.
Metal Chem Inc. has developed processes for Powder Coating Application Compliant with the Following Specifications following Standard and Corona Powder Deposition:
MIL-PRF-32348 Powder Coating, Camouflage Chemical Agent Resistant Systems
79P020011 LMC Process Specification for Powder Coating
79P050000 LMC Finish Specification, Standard General Process
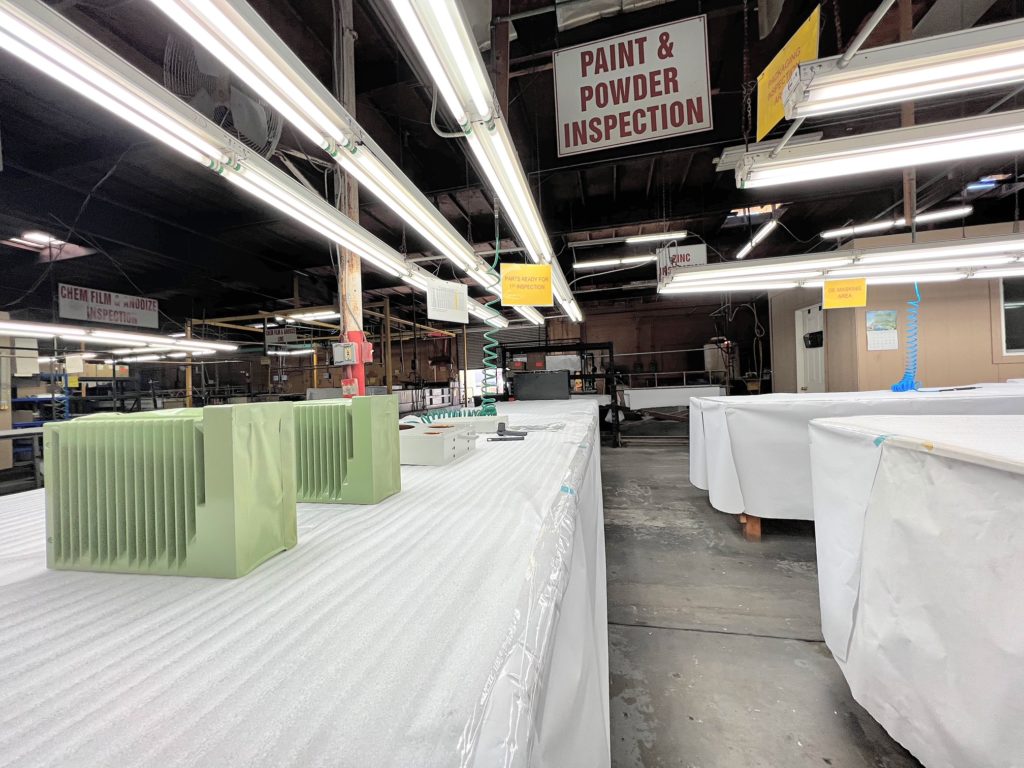
Powder Coating
Quality System
With a facility that boasts more than 15,000 square feet, our headquarters includes an in-house laboratory and state-of-the-art technology that’s unparalleled in the metal application industry. You can feel confident that your project is in the hands of experts – our team of control managers has decades of experience in the science of metal finishing, metal plating, and chemistry.
Quality Criteria for Solution Analysis and Testing
- B10 – Adhesion Testing
- B14 – Conductivity Testing
- B16 – Coating Thickness Measurement.
- B21 – Paint Color and Gloss Testing
- B22 – Solvent Resistance Testing
- B23 – Other Testing In Support of AC7108
Powder Coating Quality Control
From Start To Finish
1
Pretreatment + Masking
At Metal Chem, we take the necessary steps to prep your metal prior to the powder coating application. If masking is required, our team includes dedicated experts that handle the masking in-house.
2
Metal Application
Metal Chem Inc. maintains the appropriate process controls for our chemical conversion and electroplating processes which require surface cleaning, titration, coating weights, pH, and TDS verification.
3
QA Inspection
Metal Chem uses sophisticated process controls and analysis to ensure all of our final products meet the standards of our accreditations and mil-spec testing validation requirements.
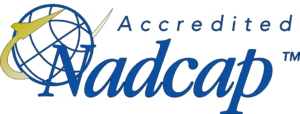
Who We Help
Aerospace & Military Metal Applications Approvals
Since 1991, Metal Chem Inc. has become one of the premiere metal plating and finishing companies in the country. Our NADCAP accreditation has allowed us to proudly fulfill the metal application needs of top technology pioneers in the aerospace, military and naval industries. As an industry leader in spec plating and metal finishing, our team has decades of experience handling complex projects that require a sophisticated level of detail.
Industries We Serve
You ask, we answer
Find answers to the most frequently asked questions about the powder coating process.
Type I coatings are primer coatings applied and cured using the powder coat process. These primer coatings are intended for use on properly cleaned and pretreated steel and aluminum, meeting unique military requirements. These requirements include adhesion to a wide variety of metals, flexibility, corrosion resistance, and resistance to leaking fluids.
Type II coatings are primer coatings designed for interior use as a one coat system having the corrosion resistance of the type I and having the color and gloss of the interior finishes. The color and gloss of the type II powder coat primer may be characteristic of the interior topcoat color as designated by FED-STD-595. Examples of the commonly used interior colors for tactical equipment are color numbers 17925 and 24533.
Type III coatings are finish coatings applied and cured using the powder coat process. They are intended to provide surfaces that are easily and effectively decontaminated after exposure to liquid chemical agents. It may be used in areas where VOCs and VOHAPs are regulated. It is applied over epoxy primers (conforming to the latest revision of MIL-PRF-23377, MIL-DTL-53022, MIL-DTL-53030, MIL-DTL-53084, the type I coating in this specification or MIL-PRF-85582), depending on the application and substrate.
Metal Chem Inc. has developed processes for Powder Coating Application Compliant with the following specifications following Standard and Corona Powder Deposition:
MIL-PRF-32348 – Powder Coating, Camouflage Chemical Agent Resistant Systems
79P020011 – LMC Process Specification for Powder Coating
79P050000 – LMC Finish Speciation, Standard General Process
Our conformal coating process includes the masking of the required areas to remain free of conformal coating material base on the design documentation, and counts with dedicated spray booths to prevent cross contaminations among the different types processed. All the assemblies are 100% visually inspected under UV light to ensure that every assembly complies with IPC-A-610 and or J-STD-001 Class 3 requirements.
Powder coating is a high-quality finish found on thousands of products you come in contact with each day. Powder coating protects the roughest, toughest machinery as well as the household items you depend on daily. It provides a more durable finish than liquid paints can offer, while still providing an attractive finish. Powder coated products are more resistant to diminished coating quality as a result of impact, moisture, chemicals, ultraviolet light, and other extreme weather conditions. In turn, this reduces the risk of scratches, chipping, abrasions, corrosion, fading, and other wear issues.
Get in Touch
Phone
(818) 727-9951
info@metalcheminc.com
Address
21514 Nordhoff Street
Chatsworth, CA 91311