ZINC Plating
per ASTM-B633.
Type I
As-Plated Without Supplementary Treatments
Type II
With Colored Chromate Coatings
Type III
With Colorless Chromate Conversion Coatings
Type IV
With Phosphate Conversion Coatings
Zinc Plating Overview
The zinc plating process provides an electrodeposited zinc coating that mitigates corrosion of iron and steel articles in order to extend the service life of parts. The service life is reduced due to the lack of protection for the iron or steel substrate resulting in corrosion of the substrate.
Types Of Zinc Plating We Provide
Metal Chem Inc. has developed an immersion process in full compliance with the zinc specification along with Hydrogen Embrittlement Treatment Required for high strength steels above 1200 MPa (39 HCR) as well as surface hardened parts.
Metal Chem Inc. is proud to provide industrial metal plating finishes that meet the requirements of general industry standards. Because of the sacrificial nature of zinc plating, different types and thicknesses have been developed over time to serve a multitude of applications. Some environments are harsher than others and as such require further protection.
ASTM B633 is a broad specification covering electrodeposited zinc coating applied to iron or steel. It is the most common standard for zinc plating and has four classifications for each of the types of electroplated zinc. Each classification specifies which supplemental treatment or chromate to apply and the plating thickness according to the type of environment.
The most standard type of zinc plating is known as Type I – this means the process is as-plated without supplementary treatments.
Zinc coating with colorful chromate passivation is know as Type II zinc plating. Colorful chromate coatings give corrosion resistance ability with a 96 hour salt spray minimum.
Zinc plating with colorless chromate conversion coatings is known as Type IV according to ASTM standards. A 12-hour salt spray minimum is required for colorless chromate conversion coatings.
According to ASTM standards, Type IV zinc plating is done with a phosphate conversion coating.
Metal Chem Inc. has developed processes to provide the following finishes:
- Clear Chromate
- Gold Chromate
- Phosphate
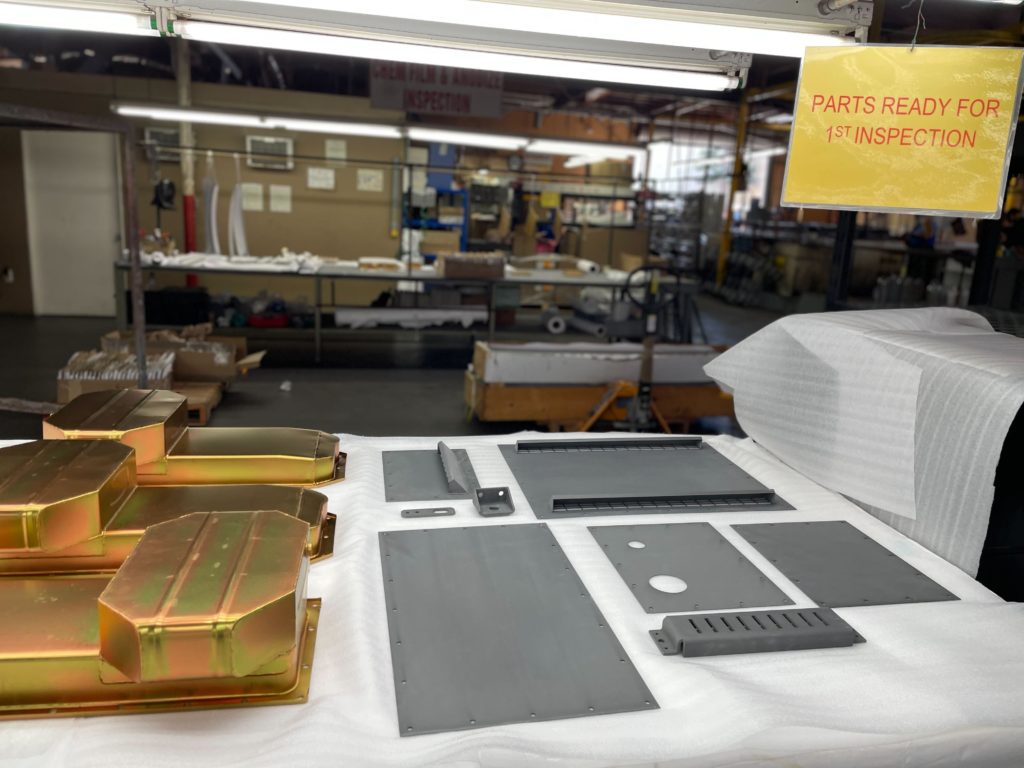
ZINC Plating
Quality System
With a facility that boasts more than 15,000 square feet, our headquarters includes an in-house laboratory and state-of-the-art technology that’s unparalleled in the metal application industry. You can feel confident that your project is in the hands of experts – our team of control managers has decades of experience in the science of metal finishing, metal plating, and chemistry.
Quality Criteria for Solution Analysis and Testing
- B10 – Adhesion Testing
- B14 – Conductivity Testing
- B16 – Coating Thickness Measurement.
- B21 – Paint Color and Gloss Testing
- B22 – Solvent Resistance Testing
- B23 – Other Testing In Support of AC7108
Zinc Plating Quality Control
From Start To Finish
1
Metal Prep & Masking
At Metal Chem, we take the necessary steps to prep your metal prior to the zinc plating application. If masking is required, our team includes dedicated experts that handle the masking in-house.
2
Metal Application
Metal Chem Inc. maintains the appropriate process controls for our chemical conversion and electroplating processes which require surface cleaning, titration, coating weights, pH, and TDS verification.
3
QA Inspection
Metal Chem uses sophisticated process controls and analysis to ensure all of our final products meet the standards of our accreditations and mil-spec testing validation requirements.
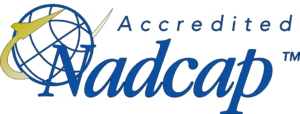
Who We Help
Aerospace & Military Metal Applications Approvals
Since 1991, Metal Chem Inc. has become one of the premiere metal plating and finishing companies in the country. Our NADCAP accreditation has allowed us to proudly fulfill the metal application needs of top technology pioneers in the aerospace, military and naval industries. As an industry leader in spec plating and metal finishing, our team has decades of experience handling complex projects that require a sophisticated level of detail.
Industries We Serve
You ask, we answer
Find answers to the most frequently asked questions about the zinc plating process.
A process known as zinc plating is frequently used to protect metals such as iron and steel against the relentless forces of corrosion. Zinc plating involves the electrodeposition of a thin coating of zinc metal onto the surface of another metal object, known as a substrate. The zinc coating creates a physical barrier that prevents rust from reaching the underlying metal surface. Zinc is chosen because of its innate ability to fight corrosion.
Metal Chem adheres to the ASTM B633, a broad specification covering electrodeposited zinc coating applied to iron or steel. It is the most common standard for zinc plating and has four classifications for each of the types of electroplated zinc. Each classification specifies which supplemental treatment or chromate to apply and the plating thickness according to the type of environment.
One of the most important benefits of zinc plating is that it will significantly increase the corrosion resistance of the underlying substrate. In addition to forming a physical barrier, the zinc serves as a sacrificial coating. This means that the zinc coating will corrode instead of the metal substrate that it protects.
Zinc can provide a corrosion-resistant coating on smaller metal parts such as nuts, bolts, screws and fasteners. In general, most hardware parts are coated with zinc. Zinc plating has also gained widespread use in the automotive industry as a means of protecting parts such as power steering components.
Additionally, zinc plating is used in the production of tanks, armored personnel carriers and other heavy military vehicles. Zinc plating can also serve as a protective undercoating prior to painting, as it can promote greater paint adhesion.
Get in Touch
Phone
(818) 727-9951
info@metalcheminc.com
Address
21514 Nordhoff Street
Chatsworth, CA 91311